Requirements for Personal Protective Equipment (PPE)
Personal Protective Equipment (PPE) is essential for protecting workers from workplace hazards that could cause injury, illness, or exposure to dangerous materials. Proper PPE selection, usage, and maintenance ensure that workers remain safe and compliant with occupational safety regulations.
This guide outlines PPE requirements, regulatory standards, selection criteria, training, and maintenance protocols across different industries.
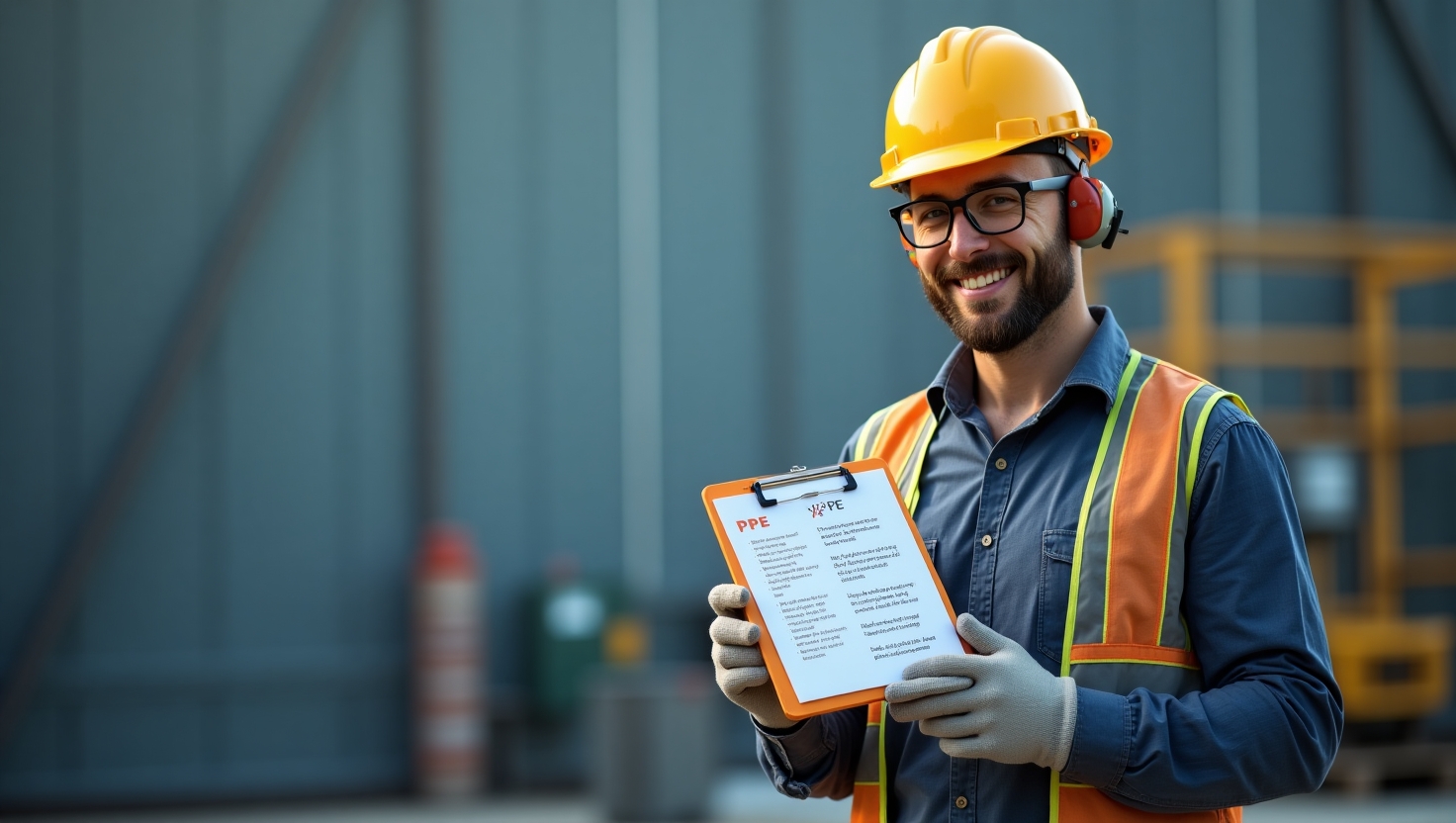
Legal and Regulatory Requirements for PPE
Occupational Safety Standards
Different regulatory bodies set standards for PPE usage to ensure worker safety in various industries.
- Occupational Safety and Health Administration (OSHA)
- Requires employers to provide, maintain, and train workers in PPE use.
- PPE must comply with OSHA 29 CFR 1910 Subpart I (General Industry) and 1926 Subpart E (Construction) regulations.
- Centers for Disease Control and Prevention (CDC)
- Establishes PPE guidelines for healthcare settings, infection control, and disease prevention.
- PPE is critical in preventing exposure to bloodborne pathogens, airborne diseases, and hazardous materials.
- Food and Drug Administration (FDA)
- Regulates medical-grade PPE, including masks, gloves, and gowns, ensuring proper filtration and material quality.
- American National Standards Institute (ANSI) & National Institute for Occupational Safety and Health (NIOSH)
- Develops performance and testing standards for PPE, such as respirators, safety glasses, and hearing protection.
Employers must ensure that PPE meets the certification and compliance standards set by these agencies.
General PPE Requirements for Workplace Safety
To be effective, PPE must meet the following criteria:
- Proper Fit and Comfort – PPE should fit securely and comfortably to allow free movement without exposing workers to hazards.
- Durability and Strength – PPE must be made from materials resistant to specific workplace hazards (chemicals, heat, sharp objects, etc.).
- Compatibility with Other PPE – Equipment should be compatible with additional safety gear, such as respirators worn with eye protection.
- Regular Inspection and Maintenance – PPE must be cleaned, stored, and replaced as needed to ensure continued protection.
- Training and Proper Use – Workers must understand how to wear, adjust, and remove PPE correctly to maintain safety.
Employers are responsible for providing the correct PPE, enforcing its use, and ensuring that all equipment is up to standard.
PPE Requirements by Category
Head Protection
Requirements:
- Must meet ANSI Z89.1 standards for impact resistance.
- Hard hats should be shock-absorbing and resistant to penetration.
- Must be adjustable and fit snugly without causing discomfort.
- Should be inspected for cracks, dents, and wear before each use.
Common PPE:
- Hard hats for construction, manufacturing, and electrical work.
- Welding helmets for eye and face protection from sparks and UV radiation.
- Bump caps for low-hazard work areas with head clearance concerns.
Eye and Face Protection
Requirements:
- Must meet ANSI Z87.1 standards for impact resistance.
- Should provide a clear line of sight without fogging.
- Safety glasses must have side protection in high-risk areas.
- Goggles and face shields should be anti-scratch and shatter-resistant.
Common PPE:
- Safety glasses for general eye protection.
- Goggles for chemical handling and dust exposure.
- Face shields for welding, grinding, and medical procedures.
Respiratory Protection
Requirements:
- Must comply with OSHA 29 CFR 1910.134 for workplace respiratory protection.
- Respirators should be NIOSH-certified to filter airborne contaminants.
- Fit testing is required for tight-fitting respirators such as N95 masks.
- Must be stored properly in a clean, dry place.
Common PPE:
- N95 masks for airborne particles and infections.
- Half-face and full-face respirators for chemical vapors and toxic fumes.
- Powered Air-Purifying Respirators (PAPRs) for high-risk environments.
Hearing Protection
Requirements:
- Must comply with OSHA’s hearing conservation program (29 CFR 1910.95).
- Noise reduction rating (NRR) must match the level of workplace noise exposure.
- Should be comfortable and adjustable for long-term use.
Common PPE:
- Foam earplugs for temporary noise reduction.
- Reusable earplugs for consistent workplace noise exposure.
- Earmuffs for loud industrial or construction settings.
Hand and Arm Protection
Requirements:
- Must be chemical-resistant, cut-resistant, or heat-resistant depending on the job.
- Should allow for manual dexterity without compromising protection.
- Disposable gloves must be changed frequently to maintain hygiene.
Common PPE:
- Latex and nitrile gloves for medical and laboratory work.
- Leather gloves for construction and heavy equipment handling.
- Cut-resistant gloves for metalworking and glass handling.
Body Protection
Requirements:
- Must cover all exposed skin areas to prevent injuries.
- Fire-resistant clothing should meet NFPA 70E standards for electrical safety.
- High-visibility clothing must meet ANSI/ISEA 107 for construction zones.
Common PPE:
- High-visibility vests for roadwork and night shifts.
- Flame-resistant clothing for electricians and fire hazards.
- Full-body coveralls for hazardous material handling.
Foot and Leg Protection
Requirements:
- Must meet ASTM F2413 standards for impact and compression resistance.
- Should be slip-resistant in wet or oily environments.
- Electrical hazard (EH) boots should protect against shock and conductive risks.
Common PPE:
- Steel-toe boots for heavy-duty construction and warehousing.
- Chemical-resistant boots for laboratory and hazardous material handling.
- Slip-resistant shoes for hospital and food industry workers.
Fall Protection
Requirements:
- Must comply with OSHA 1926.502 for construction fall protection.
- Full-body harnesses should be snug but comfortable for extended wear.
- Anchor points must support at least 5,000 lbs of force.
Common PPE:
- Full-body harnesses for work at heights above six feet.
- Lanyards and lifelines for workers using scaffolding or platforms.
- Safety nets for fall prevention in high-risk zones.
PPE Training and Worker Responsibilities
Employers must provide PPE training to ensure that workers understand:
- When and why PPE is necessary for their job.
- How to properly wear, adjust, and remove PPE.
- How to inspect PPE for damage before each use.
- Proper cleaning and storage of reusable PPE.
- How to report damaged or defective PPE to supervisors.
Workers are responsible for wearing PPE consistently, following safety protocols, and maintaining their equipment.
Common Challenges in PPE Implementation
While PPE is required across many industries, several factors affect its proper use and effectiveness.
Lack of Compliance and Proper Usage
One of the most significant challenges with PPE is non-compliance due to:
- Discomfort or lack of proper fit, leading workers to remove or adjust PPE frequently.
- Lack of training on how to wear, remove, and maintain PPE correctly.
- Overconfidence, where experienced workers underestimate risks and fail to wear PPE.
Employers must enforce PPE use through regular training, monitoring, and disciplinary actions for non-compliance.
PPE Supply Shortages and Accessibility
During global crises like the COVID-19 pandemic, PPE shortages affected hospitals, industries, and emergency responders. Challenges in PPE supply include:
- Dependence on international supply chains, leading to delays.
- Increased demand causing price surges and supply gaps.
- Low-income workplaces struggling to afford high-quality PPE.
To combat shortages, companies should maintain emergency stockpiles, establish local PPE manufacturing options, and use reusable PPE when possible.
PPE Comfort and Worker Fatigue
Many workers avoid wearing PPE for extended periods due to:
- Excessive heat buildup, especially with full-body suits and respirators.
- Restricted movement, making tasks more difficult.
- Pressure points from tightly fitted masks, goggles, and harnesses.
PPE manufacturers are focusing on ergonomic designs, better ventilation, and lightweight materials to improve comfort while maintaining protection.
Inadequate PPE Disposal and Environmental Impact
The widespread use of disposable PPE has raised concerns about waste management and environmental pollution. Common PPE disposal issues include:
- Improper disposal of masks, gloves, and gowns, leading to public health risks.
- Accumulation of PPE waste in landfills and oceans, affecting wildlife.
- Lack of recycling options for PPE made from synthetic materials.
Solutions include adopting biodegradable PPE, reusable alternatives, and hospital-grade recycling programs to reduce waste.
Emerging Trends and Future Developments in PPE
To address PPE challenges, researchers and manufacturers are developing new technologies and sustainable solutions.
Smart PPE with Technology Integration
Advancements in smart PPE help monitor worker safety using sensors and connectivity features. Examples include:
- Wearable PPE with real-time monitoring to detect temperature, humidity, and exposure to harmful gases.
- Respirators with smart filtration systems, adjusting airflow based on user activity.
- Augmented reality (AR) face shields, displaying safety instructions or hazard alerts for workers.
These innovations improve safety compliance and reduce workplace injuries through proactive monitoring.
Eco-Friendly and Reusable PPE
Sustainability in PPE design is a growing priority, with manufacturers developing:
- Biodegradable masks and gloves, reducing plastic waste.
- Reusable face shields and respirators with replaceable filters.
- Sustainable PPE manufacturing, using recycled materials to lower carbon footprints.
Industries adopting green PPE solutions contribute to both environmental conservation and cost reduction.
Customization and Ergonomic PPE Designs
Manufacturers are focusing on custom-fit PPE to improve comfort, efficiency, and long-term usability. Innovations include:
- Adjustable and form-fitting respirators for better seal and comfort.
- Lightweight yet durable materials that enhance breathability.
- Gender-specific PPE for better ergonomics and proper fit.
Custom-designed PPE improves worker compliance and reduces fatigue, increasing workplace productivity.
Advanced Material Science in PPE
Researchers are developing next-generation materials for enhanced PPE protection. Some advancements include:
- Self-cleaning PPE fabrics, preventing contamination buildup.
- Graphene-based face masks, offering better filtration and breathability.
- Nanotechnology coatings, making PPE more resistant to chemicals and heat.
These material advancements extend PPE lifespan, improve performance, and enhance safety in high-risk industries.
The Future of PPE in Various Industries
Healthcare and Medical PPE Innovations
- Self-sterilizing gloves and masks with antimicrobial coatings.
- Smart PPE tracking to monitor hospital staff exposure to infections.
- AI-assisted PPE supply management, ensuring adequate stock levels during health crises.
Construction and Industrial PPE Advancements
- Helmets with built-in impact sensors, alerting supervisors of worker injuries.
- Exoskeleton suits to reduce strain on workers’ bodies.
- Enhanced heat-resistant and flameproof clothing for hazardous environments.
Chemical and Hazardous Material PPE Evolution
- Self-sealing hazmat suits, preventing leaks in high-risk settings.
- Advanced respirators capable of detecting airborne toxins in real-time.
- Enhanced chemical-resistant gloves, reducing material breakdown over time.
These advancements will redefine PPE effectiveness, making workplaces safer and more sustainable.
Conclusion
Personal Protective Equipment (PPE) is essential in every industry to prevent workplace injuries and health risks. Employers must ensure that PPE meets regulatory standards, is properly maintained, and that workers receive proper training. By following these requirements, businesses can create a safer work environment, reduce accident rates, and ensure compliance with occupational safety laws.