The Crucial Role of Personal Protective Equipment (PPE) in the Workplace
Imagine stepping onto a bustling construction site without a hard hat or entering a hospital room with a contagious patient without gloves or a mask. It sounds risky, right? That’s because it is. Personal Protective Equipment (PPE) serves as the frontline defense against workplace hazards, ensuring that employees can perform their duties safely. In this comprehensive guide, we’ll delve into the importance of PPE, the consequences of neglecting it, and real-world examples that underscore its significance.
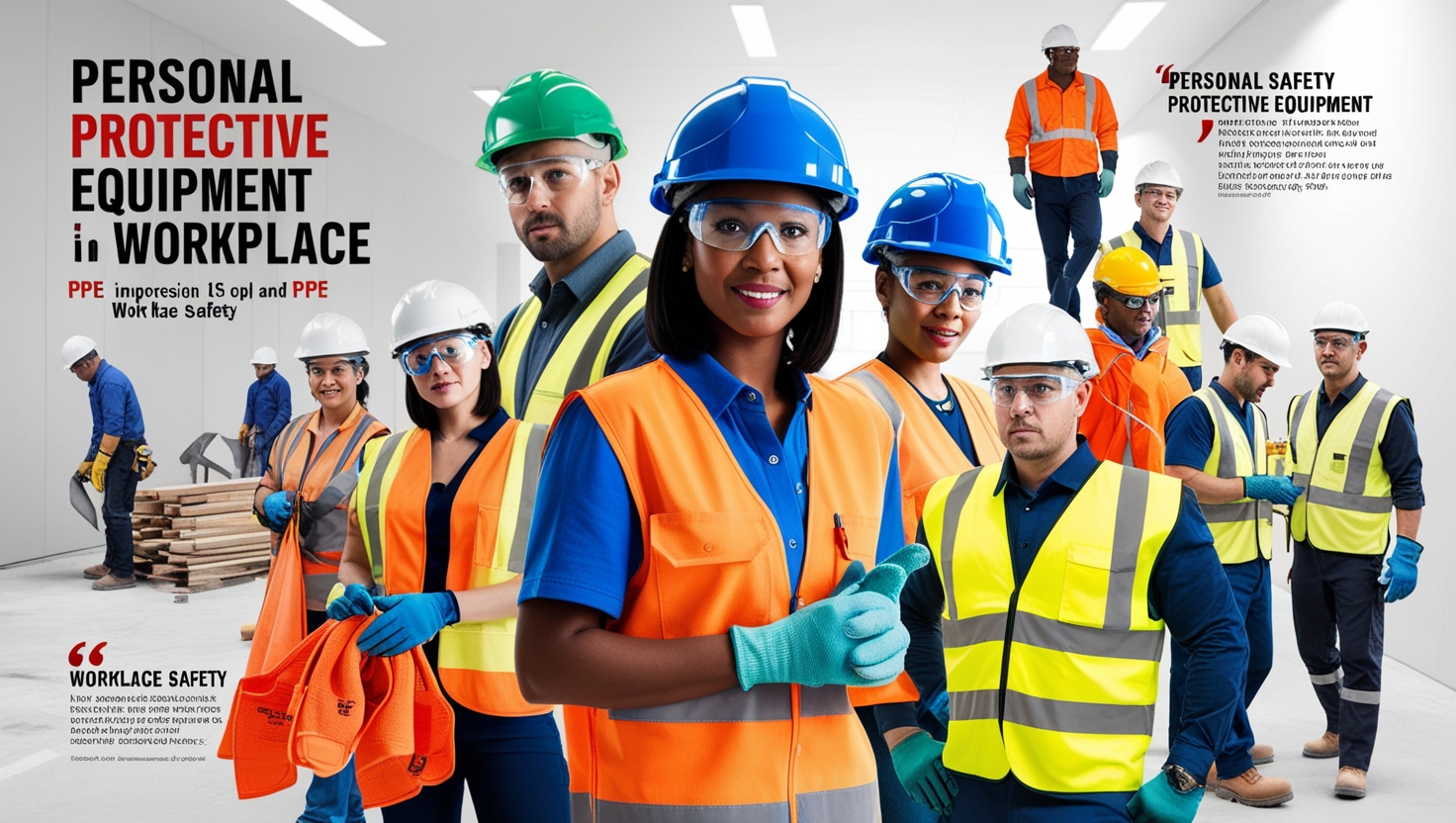
Understanding Personal Protective Equipment (PPE)
Personal Protective Equipment (PPE) encompasses a range of gear designed to protect workers from various hazards. This includes items like helmets, gloves, goggles, earplugs, respirators, and protective clothing. The primary purpose of PPE is to minimize exposure to risks that can cause serious workplace injuries or illnesses resulting from contact with physical, chemical, radiological, mechanical, or other hazards.
The Importance of PPE in the Workplace
- Prevention of Injuries and Illnesses: PPE acts as a barrier between the worker and potential hazards. For instance:
- Head Protection: Hard hats protect against falling objects or accidental head bumps.Eye Protection: Safety goggles shield the eyes from chemical splashes, flying debris, or harmful radiation.Respiratory Protection: Masks and respirators prevent the inhalation of hazardous substances like dust, fumes, or infectious agents.
- Legal and Regulatory Compliance: Occupational safety regulations mandate the use of PPE in various industries. Employers are legally obligated to provide suitable PPE and ensure its proper use. Non-compliance can lead to severe penalties, legal actions, and a tarnished reputation. According to the Occupational Safety and Health Administration (OSHA), employers must protect their employees from workplace hazards that can cause injury. Source
- Enhanced Workplace Productivity: A safe work environment fosters employee confidence and efficiency. When workers are assured of their safety through the provision of adequate PPE, they are more likely to perform their tasks effectively, leading to increased productivity and morale.
Consequences of Neglecting PPE
Failing to use or provide appropriate PPE can have dire consequences:
- Increased Risk of Accidents and Health Hazards: Without PPE, employees are vulnerable to:
- Physical Injuries: Such as cuts, burns, fractures, or amputations.
- Chemical Exposures: Leading to skin irritations, respiratory problems, or systemic poisoning. Hearing Damage: Due to prolonged exposure to high noise levels without ear protection.
- Legal and Financial Repercussions: Employers who fail to enforce PPE usage may face:
- Legal Penalties: Including fines and sanctions from regulatory bodies.Increased Insurance Premiums: Due to a higher incidence of workplace accidents.Compensation Claims: From employees who suffer injuries or illnesses due to inadequate protection.
- Diminished Employee Morale and Trust: A lack of proper protective measures can lead to:
- Decreased Job Satisfaction: Employees may feel undervalued and unprotected.Higher Turnover Rates: Workers are likely to leave environments where they feel their safety is compromised.Damage to Company Reputation: News of workplace accidents can tarnish a company’s public image.
Real-World Examples Highlighting the Importance of PPE
- Construction Industry: In Sydney, construction workers on the Metro project were exposed to silica dust levels exceeding safety standards by up to 208 times. This exposure, without adequate respiratory protection, poses severe health risks, including silicosis and lung cancer.
- Healthcare Sector: During the COVID-19 pandemic, delays in donning PPE critically impacted patient care. Ambulance crews, instructed to wear PPE upon arrival at scenes, faced minute-long delays that may have cost lives. This underscores the need for readily accessible and properly fitted PPE in emergency healthcare settings.
- Agricultural Sector: A British backpacker working on a cattle station suffered a severe injury leading to arm amputation due to inadequate safety measures and lack of proper PPE. This incident highlights the necessity of appropriate protective gear and safety protocols in agricultural settings.
Addressing Common Barriers to PPE Usage
Despite its importance, PPE usage faces several challenges:
- Discomfort and Inconvenience: Some workers find PPE uncomfortable or cumbersome, leading to reluctance in usage. Employers can address this by:
- Providing Ergonomically Designed PPE: Ensuring gear is comfortable and fits properly.
- Offering Training: Educating employees on the correct use and adjustment of PPE to enhance comfort.
- Lack of Awareness: Employees may not fully understand the risks associated with their tasks or the protective benefits of PPE. Regular training sessions and safety briefings can bridge this knowledge gap.
- Cultural and Behavioral Factors: In some workplaces, there may be a culture of neglecting safety gear due to peer pressure or a false sense of invincibility. Cultivating a safety-first culture, where PPE usage is the norm and reinforced by leadership, can mitigate this issue.
Employer Responsibilities in PPE Implementation
Employers play a pivotal role in ensuring the effective use of PPE in the workplace. Their responsibilities include:
Providing the Right PPE
Employers must ensure that all workers have access to appropriate PPE for their specific tasks. This includes:
- Supplying gear that meets safety standards.
- Ensuring PPE is available in various sizes for a proper fit.
- Replacing damaged or expired PPE promptly.
Conducting Risk Assessments
Before issuing PPE, employers should assess potential hazards in the workplace. This helps identify:
- Which risks require protective equipment.
- The type of PPE necessary for each job role.
- How often PPE should be inspected and replaced.
Training Employees on PPE Usage
Even the best PPE is useless if workers don’t know how to wear it properly. Training should cover:
- How to correctly wear, adjust, and remove PPE.
- The importance of PPE in preventing injuries.
- Proper storage and maintenance of equipment.
Enforcing PPE Policies
Employers must ensure PPE compliance by:
- Establishing clear safety guidelines.
- Monitoring employees for consistent PPE usage.
- Implementing consequences for failing to wear required gear.
Encouraging a Safety-First Culture
Safety isn’t just about rules-it’s about mindset. When leadership actively promotes PPE use, employees are more likely to take it seriously. Employers can:
- Recognize and reward PPE compliance.
- Lead by example-managers should wear PPE too.
- Encourage employees to report safety concerns.
The Cost of Non-Compliance
Some companies try to cut corners by reducing safety measures, but the financial and human costs of neglecting PPE far outweigh any short-term savings.
Financial Penalties
Regulatory agencies impose heavy fines on businesses that fail to provide or enforce PPE. For example:
- OSHA can fine companies thousands of dollars per violation.
- Repeat offenders may face lawsuits or be shut down entirely.
Increased Insurance Costs
Workplace injuries lead to higher insurance premiums. Businesses that fail to protect workers may face:
- Increased workers’ compensation claims.
- Higher costs for medical treatment and recovery.
- Potential legal settlements if employees sue for negligence.
Productivity Losses
Injured workers can’t perform their duties, leading to:
- Delays in project completion.
- Increased workload on other employees.
- Potential hiring costs if replacements are needed.
Reputation Damage
News of workplace accidents spreads quickly. Companies that don’t prioritize employee safety may struggle to:
- Attract skilled workers who value safe conditions.
- Retain current employees who feel unprotected.
- Maintain customer trust and brand loyalty.
How PPE Compares to Other Safety Measures
Some employers argue that engineering controls and administrative policies should take precedence over PPE. While these measures are important, PPE serves as the last line of defense when other precautions fail.
Safety Measure | How It Works | Effectiveness |
---|---|---|
Engineering Controls | Modifies the workplace to remove hazards (e.g., ventilation, noise barriers). | Reduces hazards but may not eliminate all risks. |
Administrative Controls | Changes work procedures to minimize exposure (e.g., rotating shifts, training). | Helps reduce risks but depends on worker compliance. |
PPE | Creates a barrier between workers and hazards (e.g., helmets, gloves, masks). | Essential when other controls aren’t enough. |
While a combination of safety measures is ideal, PPE remains crucial in hazardous environments.
How YouTube Money Calculator Relates to PPE
You may be wondering what does a YouTube Money Calculator have to do with PPE? The connection lies in workplace safety education and awareness.
Many businesses and safety advocates use platforms like YouTube to:
- Demonstrate proper PPE usage.
- Share real-life safety incidents.
- Provide training on risk prevention.
Creators who focus on workplace safety can monetize their content, making educational PPE videos both informative and profitable.
Using a YouTube Money Calculator, safety content creators can estimate earnings based on views, engagement, and ad revenue. This encourages more professionals to share vital workplace safety information, ultimately reducing accidents and increasing awareness.
For example, a YouTube safety channel with 500,000 monthly views could earn between $1,000 to $3,000 depending on ad rates. This proves that promoting PPE awareness isn’t just beneficial for workers—it can also be a sustainable source of income for content creators.
Future of PPE: Advancements and Trends
PPE technology is evolving to offer better protection and comfort. Some innovations include:
- Smart Helmets
- Built-in sensors to detect impacts.
- Heads-up displays showing safety data.
- Real-time communication with teammates.
- Self-Cleaning Fabrics
- Antimicrobial coatings reduce contamination risks.
- Waterproof materials keep workers dry in extreme conditions.
- AI-Powered Safety Gear
- Wearables that monitor vital signs.
- Alerts that notify supervisors if a worker is in danger.
- Augmented reality (AR) glasses for hands-free instructions.
Investing in next-gen PPE ensures long-term workplace safety and compliance with emerging safety standards.
What are the latest advancements in PPE technology?
Recent innovations in PPE technology focus on improving protection, comfort, and sustainability. Some of the most notable advancements include:
- Smart PPE: Embedded sensors that monitor environmental conditions (e.g., gas levels, heat stress) and track workers’ locations in real time. Firefighters and construction workers benefit from this technology to prevent accidents.
- Advanced Materials: Nanofibers enhance breathability in masks, nano-coatings improve water and chemical resistance, and self-decontaminating fabrics neutralize bacteria and viruses upon contact.
- Ergonomic Enhancements: Modular PPE that adapts to specific tasks, lightweight materials that reduce strain, and better-fitting designs ensure comfort and long-term usability.
- Augmented Reality (AR) Integration: AR-enabled helmets and goggles display critical safety information, aiding workers in high-risk environments such as industrial manufacturing and mining.
- Eco-Friendly PPE: Sustainable, biodegradable materials and reusable PPE help reduce environmental impact while maintaining safety standards.
How do different industries enforce PPE compliance?
Different industries enforce PPE compliance through a combination of regulations, training, and penalties:
- Construction: OSHA mandates safety helmets, gloves, and boots. Regular inspections ensure workers wear PPE, and violations can lead to fines or worksite shutdowns.
- Healthcare: Hospitals require strict adherence to PPE use, especially for infectious disease control. Regular audits and immediate disciplinary actions for non-compliance reinforce compliance.
- Manufacturing & Chemical Plants: Safety officers monitor PPE use through surveillance and inspections. Some companies implement electronic PPE tracking to ensure workers are protected at all times.
- Oil & Gas: PPE policies are strictly enforced due to the high risk of explosions and chemical exposure. Safety drills and incentive programs encourage compliance.
- Agriculture: PPE like respirators and gloves are required when handling pesticides. Some governments provide PPE subsidies to farmers to improve adoption.
Can you provide examples of companies fined for PPE violations?
Several companies have faced significant penalties for failing to enforce PPE regulations. Some examples include:
- Amazon (Warehouse Violations, 2022-2023): Amazon faced fines for failing to provide adequate PPE in warehouses, leading to worker injuries. OSHA cited the company for exposing employees to ergonomic hazards.
- Sydney Metro Construction (Silica Dust Exposure, 2024): Workers were exposed to silica dust levels 208 times above the safety limit due to inadequate respiratory protection, leading to potential long-term health risks.
- Meat Processing Plants (COVID-19 PPE Violations, 2020-2021): Several meatpacking companies were fined for failing to provide workers with face masks and other protective equipment, leading to mass outbreaks.
- Townsville University Hospital (Security PPE Neglect, 2024): After a guard was stabbed, reports revealed that staff had been requesting stab-proof vests for over 100 days without response.
These cases highlight the importance of consistent PPE enforcement to prevent workplace injuries and illnesses.
What are the psychological barriers to consistent PPE use?
Even when PPE is available, workers sometimes resist wearing it due to psychological barriers such as:
- Perceived Invincibility: Workers with long experience in a field may underestimate risks, believing they won’t get injured.
- Comfort Issues: Bulky or uncomfortable PPE discourages regular use, especially in hot or physically demanding environments.
- Peer Pressure & Workplace Culture: If coworkers or supervisors neglect PPE, others may feel pressured to do the same.
- Lack of Immediate Consequences: Unlike an obvious injury risk, some hazards (like inhaling chemicals or loud noise exposure) don’t have immediate effects, making workers less likely to prioritize protection.
- Lack of Training: If workers don’t fully understand the risks and benefits, they may not take PPE requirements seriously.
To overcome these barriers, companies should focus on education, incentives, and providing comfortable, well-fitting PPE to improve compliance.
Final Thoughts
Personal Protective Equipment is a non-negotiable aspect of workplace safety. Both employers and employees share the responsibility of ensuring that PPE is available, worn correctly, and maintained.
By wearing PPE, workers can protect themselves from injuries, illnesses, and long-term health risks. Companies that prioritize PPE not only comply with regulations but also save money, improve morale, and maintain a positive reputation.
If you’re in a role where PPE is required wear it. If you’re an employer provide it. Safety starts with the right protection, and PPE is a simple yet effective way to ensure everyone goes home unharmed.