Electrical Safety Personal Protective Equipment (PPE): A Complete Guide
Working with electricity is dangerous. A single mistake can lead to serious injuries, fires, or even fatalities. Electrical hazards are a major concern in industries like construction, manufacturing, power plants, and utility work. One of the most effective ways to reduce risk is by using the right Personal Protective Equipment (PPE).
Electrical PPE isn’t just about compliance-it’s about protecting lives. This guide will break down:
- The essential electrical PPE you need.
- How it protects workers.
- Industry regulations and compliance.
- Real-life examples of PPE-related incidents.
- Best practices for PPE maintenance and use.
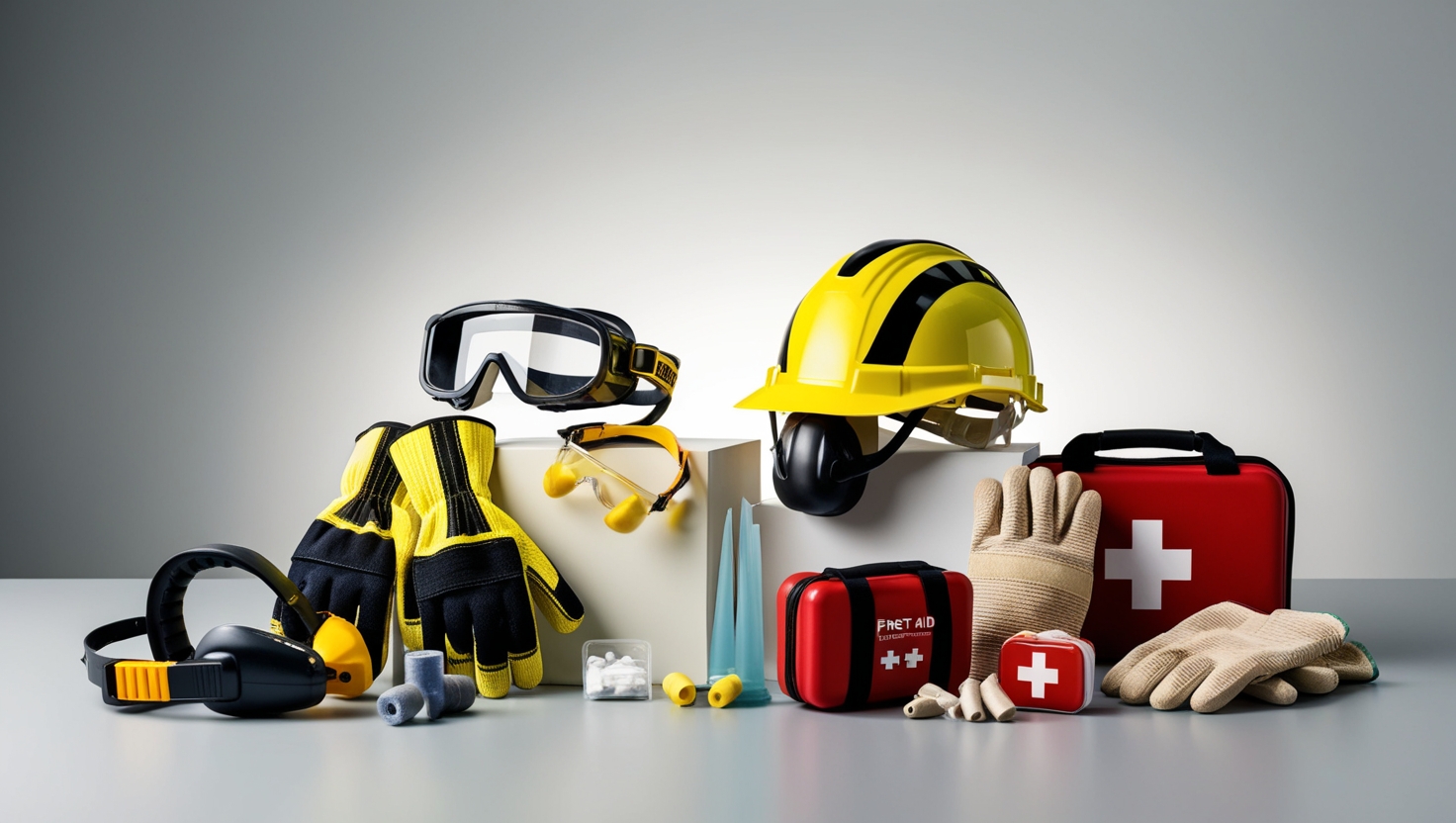
Why is Electrical Safety PPE Important?
Electrical hazards include electric shocks, burns, explosions, and fires. Unlike other workplace hazards, electricity is invisible, making it harder to detect risks before an accident happens. PPE serves as a critical barrier between the worker and potential electrical dangers.
Common Electrical Hazards Include:
- Direct Contact with Live Wires – Touching a live conductor can result in severe shocks or electrocution.
- Arc Flash – A sudden electrical discharge producing intense heat and light that can cause severe burns.
- Electromagnetic Fields (EMFs) – Long-term exposure to strong EMFs can cause health problems.
- Faulty Equipment – Old or damaged wiring and tools increase the risk of accidents.
Wearing the right PPE significantly reduces the chances of injury or death.
Essential Electrical Safety PPE
Different PPE is required based on the level of electrical hazard. Below is a breakdown of must-have electrical PPE:
PPE Type | Protection Provided | Common Applications |
---|---|---|
Insulated Gloves & Sleeves | Protect hands from electric shock | Electrical wiring, switchboards |
Arc Flash Suits | Shields against high-temperature arc blasts | Power stations, high-voltage areas |
Insulated Tools | Prevents accidental electrical contact | Maintenance of live circuits |
Face Shields & Helmets | Protects from flying debris and burns | High-voltage operations, arc flash risks |
Dielectric Boots | Prevents grounding and electric shocks | Construction, substations, wet environments |
Lockout/Tagout Equipment | Ensures circuits are de-energized before work begins | Industrial equipment maintenance |
Hearing Protection | Shields from high-decibel arc blasts | Power plants, substations |
Each piece of PPE plays a specific role in protecting workers from electrical hazards.
Compliance and Regulations
To ensure worker safety, regulatory bodies require PPE use in electrical environments. Here are some key regulations:
- OSHA 1910.269 – U.S. standard outlining electrical safety requirements in power generation, transmission, and distribution.
- NFPA 70E – Defines PPE categories based on electrical hazard levels.
- ASTM F1505 – Specifies standards for insulated hand tools.
- IEC 60903 – International standard for insulated gloves.
Employers must provide the correct PPE, conduct training, and enforce safety policies to comply with these regulations.
Real-Life PPE Incidents and Lessons Learned
Understanding real-world cases highlights why PPE matters. Here are a few incidents where PPE saved—or could have saved—lives:
- Sydney Metro Construction Incident (2024)
- Workers examining real-world cases emphasize the importance of PPE. Here are several incidents where PPE saved or could have saved lives: exposed to silica dust levels 208 times above the legal limit.
- Inadequate respiratory PPE led to severe health risks.
- This highlights the need for proper PPE enforcement in hazardous environments. Amazon PPE Violations (2022-2023)
- OSHA Examining real-world cases emphasizes the importance of PPE. Here are several incidents where PPE saved or could have saved lives: fined Amazon for failing to provide adequate PPE to warehouse workers.
- The company faced multiple safety violations leading to injuries.
- Proper PPE policies could have reduced these incidents. Townsville University Hospital (2024)
- A security guard was stabbed after staff requested stab-proof vests for over 100 days without response.
- Delayed PPE provision cost a worker’s safety.
Takeaway:
- Failing to provide PPE can lead to injuries, legal consequences, and financial losses.
- Employers must act before accidents happen, not after.
Overcoming Common PPE Challenges in the Workplace
Even with access to Personal Protective Equipment (PPE), workers sometimes fail to wear it consistently. This non-compliance increases the risk of workplace injuries, especially in high-risk environments like electrical work. Below are some common barriers to PPE use and effective solutions to address them.
Barrier: Uncomfortable or Restrictive PPE
Many workers avoid wearing PPE because it feels bulky, hot, or restrictive, making it difficult to perform their tasks efficiently.
Solution:
Invest in ergonomic PPE designed for comfort and breathability. Lightweight, well-fitted, and ventilated PPE can significantly improve compliance. Employers should also allow workers to test different PPE options to find the best fit for their needs.
Barrier: Lack of Awareness
Some workers underestimate the risks associated with their tasks or are unaware of how PPE protects them from hazards.
Solution:
Regular safety training sessions should be conducted to educate employees about the dangers of electrical work and the role PPE plays in preventing accidents. Demonstrations, real-life case studies, and visual reminders like posters can reinforce the importance of proper PPE usage.
Barrier: Poor Fit or Inadequate PPE
If PPE doesn’t fit properly or isn’t suited for the specific job, it can leave workers vulnerable to electrical shocks, burns, or arc flashes.
Solution:
Employers should provide PPE in multiple sizes and ensure each worker has the correct gear for their specific role. Regular fit testing and PPE assessments should be conducted to guarantee proper protection.
Barrier: Overconfidence in Experience
Seasoned workers may develop a sense of overconfidence and believe they don’t need PPE because they’ve “never had an accident before.”
Solution:
Implement a zero-exception PPE policy, making it mandatory for all employees, regardless of experience level. Supervisors must strictly enforce this rule and lead by example by always wearing the required PPE themselves.
Best Practices for Electrical PPE Usage
To maximize protection, workers should follow these PPE best practices:
Inspect PPE Before Each Use
PPE should be checked for any damage, including tears, cracks, or wear. A small defect in insulated gloves, arc-rated suits, or dielectric boots can compromise their effectiveness.
Follow Manufacturer Guidelines
Each type of PPE comes with specific usage instructions and lifespan recommendations. Workers must be trained to use and maintain their gear according to the manufacturer’s guidelines.
Store PPE Properly
Proper storage prevents contamination, damage, and premature degradation. Insulated gloves should be stored in protective cases, and arc flash suits should be kept clean and dry.
Train Employees Regularly
Frequent training ensures that workers remain aware of PPE protocols. Interactive safety drills and refresher courses help reinforce PPE best practices.
Monitor Compliance
Supervisors should actively enforce PPE use and correct any non-compliance immediately. Workplace safety audits and peer accountability programs can help maintain high PPE adherence.
By addressing common PPE challenges and reinforcing best practices, organizations can significantly reduce workplace hazards and protect workers from life-threatening injuries.
The Future of Electrical PPE: Innovations and Advancements
As technology continues to evolve, so does the field of electrical Personal Protective Equipment (PPE). Advancements in materials, smart technology, and artificial intelligence (AI) are transforming how workers stay safe in high-risk environments. The latest innovations aim to enhance protection, improve comfort, and increase sustainability while ensuring compliance with safety standards.
Smart Helmets with Augmented Reality (AR)
New AR-integrated helmets provide real-time safety alerts and interactive work instructions, improving situational awareness for electrical workers.
Key Features:
- Displays hazard warnings in the worker’s field of view
- Provides step-by-step guidance for complex electrical tasks
- Includes built-in cameras for remote monitoring and assistance
Impact: AR technology reduces human error, improves training efficiency, and enhances on-site decision-making.
Self-Healing Insulated Gloves
Insulated gloves are a critical defense against electrical shocks, but small tears or punctures can compromise their effectiveness. Self-healing gloves use advanced polymers that can repair minor damage on their own, extending their lifespan and maintaining protection.
Key Features:
- Automatically closes small cuts and punctures to prevent insulation failure
- Reduces the need for frequent glove replacements
- Maintains safety standards without requiring immediate disposal
Impact: This innovation improves durability, reduces PPE waste, and lowers replacement costs.
AI-Powered PPE Monitoring Systems
AI-driven PPE monitoring ensures that workers wear and use PPE correctly. Smart sensors embedded in helmets, gloves, and suits can detect improper usage and send alerts to workers and supervisors in real time.
Key Features:
- Detects if PPE is worn incorrectly or if critical gear is missing
- Uses machine learning to analyze workplace hazards and provide personalized safety recommendations
- Integrates with mobile apps and smartwatches for instant notifications
Impact: AI-powered monitoring increases PPE compliance, helps prevent human errors, and improves workplace safety culture.
Eco-Friendly and Sustainable PPE
With growing concerns over environmental impact, manufacturers are developing biodegradable and recyclable PPE options. Eco-friendly PPE helps reduce landfill waste and promotes sustainability without compromising protection.
Key Features:
- Made from biodegradable materials like plant-based fibers and recyclable synthetics
- Reduces reliance on petroleum-based plastics
- Maintains durability and protection while being environmentally responsible
Impact: Sustainable PPE reduces waste, lowers carbon footprints, and aligns with green safety initiatives.
Looking Ahead: The Future of Electrical PPE
These innovations are reshaping workplace safety by making electrical PPE more intelligent, durable, and sustainable. With smart technology, self-repairing materials, AI-driven compliance, and eco-friendly alternatives, the next generation of PPE will provide better protection while improving worker comfort and efficiency.
As industries continue to adopt these advancements, electrical safety standards will evolve to integrate new technologies, ensuring that workers remain protected, productive, and environmentally responsible.
Final Thoughts
Electrical work is dangerous, but the right PPE can make all the difference. Employers and workers must prioritize safety, enforce PPE use, and stay updated with industry regulations.
By following best practices, staying compliant, and using high-quality protective gear, electrical workers can stay safe and minimize risks in hazardous environments.