Cut-Resistant Gloves for Unmatched Protection
In the realm of workplace safety, the importance of hand protection cannot be overstated. As the last line of defense, personal safety gear plays a pivotal role in safeguarding workers’ lives and health from occupational hazards. Among these protective tools, cut-resistant gloves stand out for their effectiveness in preventing injuries from sharp objects and machinery. Recognizing potential risks in diverse work environments is crucial. At Andanda, we dedicate ourselves to understanding these dangers, valuing the insights and experiences of front-line workers. By offering professional protection solutions powered by our advanced personal protection technologies, we aim to shield workers from harm, underscoring our commitment to preventing, avoiding, or minimizing work-related injuries.
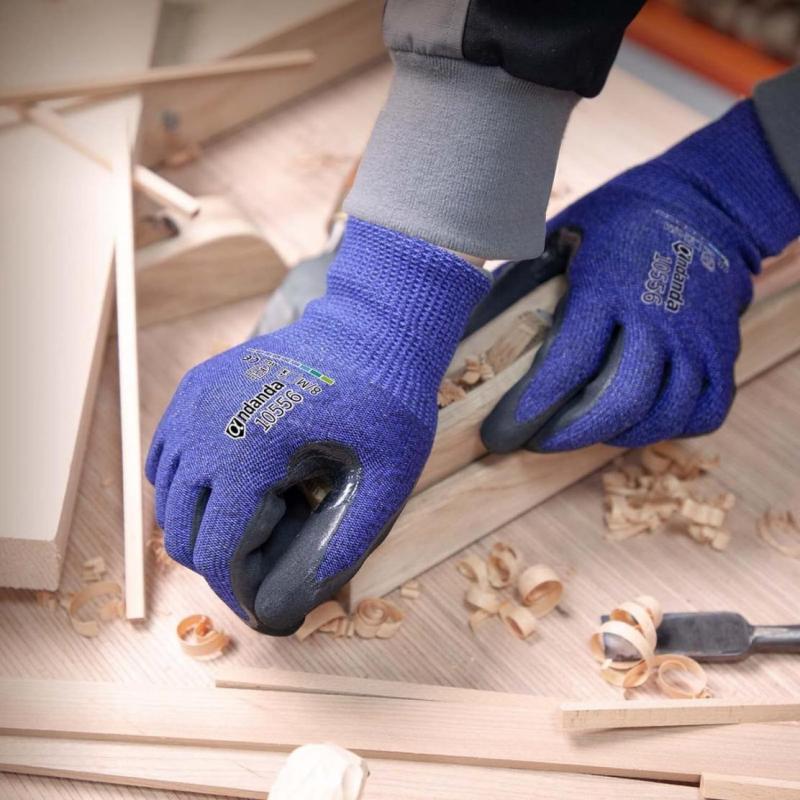
Deciphering Cut Resistance
The Essence of Cut Resistance and Its Measurement
Cut resistance denotes a material’s capacity to resist penetration by sharp objects, a fundamental property for the fabrication of cut-resistant gloves. This trait is quantified through standardized testing, which gauges the amount of force a blade can exert on the material before breaching it. This critical measure aids in the precise selection of gloves for diverse tasks, ensuring optimal protection.
Exploring Cut Resistance Levels and Their Significance
Cut resistance is categorized into levels, generally from Level 1 (minimal resistance) to Level 5 or beyond (maximum resistance), contingent on the standard referenced. Each level delineates the protective strength of gloves against cutting perils, with higher levels signifying enhanced cut resistance appropriate for more hazardous environments.
Frameworks and Certifications Defining Cut Resistance
Cut resistance is governed by two principal standards: EN388 (European standard) and ANSI/ISEA 105 (American standard). These benchmarks evaluate gloves’ resistance to cuts, abrasions, punctures, and tears, offering a comprehensive safety guideline and facilitating the selection of suitable gloves based on specific user requirements.
The Fabric of Protection: Materials and Technologies
A Survey of Materials in Cut-Resistant Gloves
The manufacture of cut-resistant gloves incorporates a spectrum of materials, each with distinct levels of protection, durability, and comfort. The material chosen directly influences the glove’s efficacy in particular scenarios.
Pioneering Materials
Synthetic fibers such as Kevlar, Dyneema, and Spectra, celebrated for their robust tensile strength and cut resistance, ensure superior protection. These fibers maintain flexibility and comfort, making them ideal for crafting gloves that guard against sharp objects.
The Role of Metal Mesh
For utmost cut resistance, metal mesh gloves are unparalleled, often employed in scenarios demanding extreme protection like meat processing. Despite their superior durability, they trade off some flexibility compared to synthetic alternatives.
Innovative Composite Materials
Composite materials blend various fibers to elevate cut resistance and durability, tailored to impart specific features such as improved grip or chemical resistance, adapting to unique protective needs.
Advancements in Glove Manufacturing Technology
Technological progress in glove production has led to gloves that are not only more resistant to cuts but also offer enhanced comfort and flexibility. This progress includes innovations in knitting technologies, coating techniques, and the integration of novel materials.
Balancing Protection, Durability, and Comfort in Material Selection
Choosing cut-resistant gloves requires weighing protection against dexterity and comfort. While high-performance fibers provide an excellent balance, they come at a cost. Metal mesh ensures unparalleled protection at the expense of comfort, whereas composite materials present a middle ground, offering customized features for specific demands.
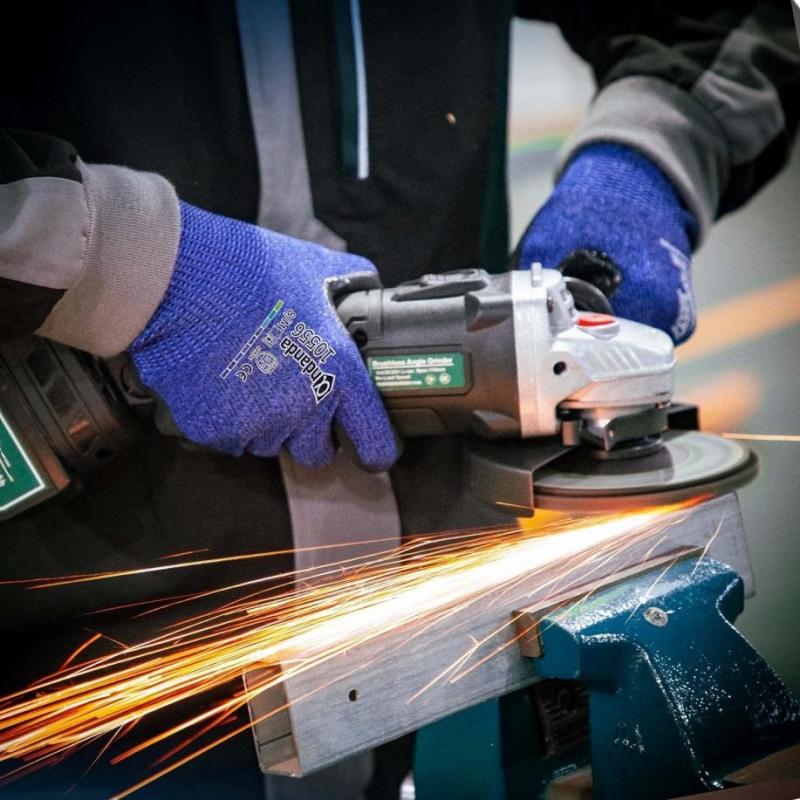
Varieties of Cut-Resistant Gloves
Coated vs. Uncoated Gloves
Coated gloves boast an additional layer over the fabric base, improving grip and resilience against chemicals or moisture. In contrast, uncoated gloves prioritize breathability and flexibility but might not offer the enhanced grip or protection against liquids that coated varieties provide.
Knit Gloves
Featuring a seamless, knitted design, knit gloves deliver a comfortable fit and agile dexterity. Constructed with advanced materials like Kevlar or Dyneema, these gloves provide superior cut resistance without compromising on comfort.
Leather Gloves
Renowned for their robustness and abrasion resistance, leather gloves afford a moderate level of cut protection. Commonly utilized in construction and metalwork, they adeptly guard against diverse hazards.
Chain Mail Gloves
Optimal for the food processing industry, particularly in meat handling, chain mail gloves excel in cut resistance. Composed of interlinked metal rings, they offer unparalleled defense against cuts from sharp instruments.
Impact-Resistant Gloves with Cut Protection
Engineered to offer dual protection, these gloves merge cut resistance with cushioning or reinforced sections to guard against impacts. Suited for demanding tasks across construction and automotive sectors, they provide extensive hand safety.
Application-Specific Gloves
Designed with specific tasks in mind, such as those in food service or glass handling, these gloves are customized to fulfill the particular needs of each application, ensuring optimal safety, agility, and sanitation.
Choosing the Appropriate Gloves
Considerations for Selection
When selecting suitable cut-resistant gloves, various aspects should be considered:
- Type of Cut Hazards: Evaluate the sharp objects and materials being handled.
- Work Environment: Take into account potential wet, oily, or temperature extremes.
- Dexterity and Sensitivity: Opt for gloves that provide the needed touch sensitivity and maneuverability.
- Size and Fit: Ensuring a proper fit is vital for safety and wearer comfort. Gloves should neither constrict nor slip.
- Deciphering Glove Labels and Ratings: Labels on gloves indicate their cut resistance level as per EN388 or ANSI/ISEA standards, aiding in the choice of gloves that meet task-specific safety requirements.
By meticulously evaluating these criteria, workers and safety professionals can identify cut-resistant gloves that best align with the demands of their specific tasks, marrying protection with dexterity and comfort.
Use Cases and Applications
Industries and Jobs That Benefit from Cut-Resistant Gloves
Cut-resistant gloves are essential in various industries to protect workers from injuries. Key sectors include:
- Manufacturing: Workers handling sharp objects or machinery require gloves to prevent cuts and abrasions.
- Construction: Protection against sharp materials and tools is crucial on construction sites.
- Food Processing: Gloves prevent cuts from knives and other sharp utensils, ensuring both worker safety and food hygiene.
- Metal Handling: Handling sharp metal objects and sheets necessitates high cut resistance to prevent lacerations.
- Automotive: Assembly and repair work involve exposure to sharp edges, requiring effective hand protection.
Real-World Scenarios
In manufacturing, a worker handling sheet metal wore cut-resistant gloves, preventing a potentially severe laceration when a piece slipped. In food processing, gloves have reduced the incidence of knife-related injuries, safeguarding employees while slicing and dicing.
Maintenance and Care
Best Practices for Cleaning and Maintaining Cut-Resistant Gloves
To ensure longevity and performance, follow these guidelines:
- Cleaning: Regularly clean gloves according to manufacturer instructions to remove contaminants that can degrade materials. Most gloves can be machine washed, but verify first.
- Drying: Allow gloves to air dry completely before the next use to prevent mildew and maintain integrity.
Inspecting Gloves for Wear and Tear
Regular inspection is crucial to detect signs of wear, such as thinning fabric, tears, or compromised seams. Any damage can significantly reduce protection, making timely inspection critical for safety.
When to Replace Cut-Resistant Gloves
Replace gloves when they show signs of significant wear or after a cut incident, even if visible damage seems minimal. Continuous exposure to hazards can weaken materials, diminishing their protective capabilities over time. Always err on the side of caution and replace gloves to ensure maximum protection.
By understanding specific applications, adhering to maintenance protocols, and recognizing when to replace gloves, users can significantly enhance safety and reduce the risk of hand injuries in hazardous work environments.
In Closing
Cut-resistant gloves stand as a fundamental component in ensuring workplace safety across various industries. By offering unparalleled protection against sharp objects and hazardous materials, they significantly reduce the risk of injuries, enabling workers to perform their duties with confidence and security. The selection of the right gloves, tailored to specific tasks and environments, alongside diligent maintenance and timely replacement, is crucial for maintaining their protective efficacy. As technology and materials evolve, the future of cut-resistant gloves promises even greater levels of protection, comfort, and dexterity. This evolution underscores the commitment to safeguarding the well-being of workers everywhere, solidifying cut-resistant gloves as an indispensable tool in the arsenal of workplace safety measures. Their role in preventing injuries not only highlights the importance of personal protective equipment but also reflects a broader commitment to fostering safer work environments for all.